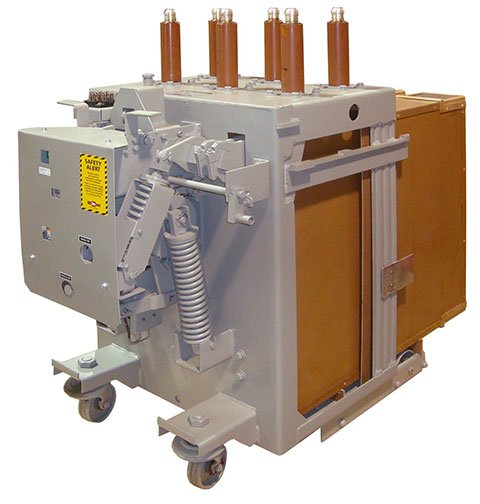
There are many situations in which you might have to consider remanufactured air circuit breakers. For example, maybe an obsolete draw-out air breaker fails and needs to be replaced. Or you may want to upgrade to solid state trip units in your breakers. Or maybe you just want them completely rebuilt instead of doing the normal preventive maintenance items in-house. Maybe you just want to have a spare breaker. Regardless of the situation, you want to make a correct and knowledgeable decision. Let’s look at factors that will help you make the right choice.
Basic Guide
Some basic remanufacturer attributes will affect your decision. These include:
- Longevity. Look for remanufacturers that have been in the business for a minimum of five years. Ten years is even better. The longer a firm has been in business, the more experience it has acquired. Seek out word-of-mouth endorsements from your peers at other locations. If they’re happy, chances are you will be too.
- Testing Capabilities. A good remanufacturer should have in-house testing capabilities and modern testing equipment. Documented test reports should be available for any work done. Testing should be done per appropriate NEMA, ANSI, and IEEE test methods.
- Warranties. All remanufacturers should guarantee their work for a period of one year, minimum. A warranty of two or three years is even better and certainly indicates confidence in repair/remanufacture capabilities.
- Exchange Capabilities. To minimize your downtime, the remanufacturer should offer you a spare breaker to use while yours is being repaired. Remember, downtime means lost revenues, which can far exceed the repair or replacement costs of the breaker in question.
- Adequate Inventory. The remanufacturer should have an adequate supply of parts in inventory or should know where to obtain those parts in a hurry. This means that any worn part can and will be replaced. It also means that you won’t have to wait for, say, an obsolete arc chute from a pre–World War II breaker.
- Integrity and Honesty. The remanufacturer should be honest, interested, and knowledgeable about your particular needs.
Creating a Rebuild Specification
Once you’ve decided that several reputable firms have the above attributes, you need to create a rebuilding specification. This is important because you want all the companies to quote on the same criteria — “apples to apples,” if you will. This will ensure that the equipment rebuild you ultimately receive will be of the quality you expect. You should specify the following as a minimum:
- Complete disassembly of the breaker. If the breaker is not completely disassembled, how will the manufacturer know if there are any worn parts that need to be replaced?
- Inspection of all worn parts. Each worn part should be inspected for physical integrity per the original equipment manufacturer’s (OEM’s) specifications.
- Replacement of worn parts as needed. This is self-explanatory but ever so important.
- Inspection of contacts. Pitted contacts should be repaired or replaced if necessary.
- Replating, repainting, and/or reinsulating of all parts as required.
- Removal of trip units to inspect for wear, clean dashpots, and refill with proper oil.
- Inspection of wiring on electrically operated breakers.
- Full lubrication of breaker.
- Reassembly of breaker per OEM’s specifications.
Electrical Testing Required
The following electrical tests, per ANSI/IEEE C37.50, should be included in your rebuild specification:
- Contact resistance test.
- Insulation resistance test: phase to ground, phase to phase, across open poles.
- Long time-delay testing determined by primary injection at 300% pickup current, per OEM specifications.
- Short time-delay testing determined by primary injection, per OEM specifications.
- Instantaneous pickup current, determined by primary injection, per OEM specifications.
- Verification of trip unit reset.